Twinkling Christmas lights transform our homes during the holiday season, yet few people know the fascinating journey these illuminating decorations take from raw materials to finished products. Inside modern manufacturing facilities, intricate machines and skilled workers combine precision engineering with time-tested techniques to create the strings of lights that bring magic to our celebrations. From the delicate process of wire drawing and bulb formation to the careful assembly of weatherproof components, each step reflects decades of innovation in holiday lighting technology. Today’s Christmas lights represent a perfect blend of traditional craftsmanship and cutting-edge manufacturing methods, producing increasingly energy-efficient and durable products that continue to evolve with advances in LED technology and sustainable production practices. Understanding how these festive illuminations are made not only reveals the complexity behind their creation but also helps consumers make more informed choices about the quality and environmental impact of their holiday decorations.
The Basic Components of Christmas Lights
Wire and Insulation
The electrical heart of Christmas lights consists of insulated copper or aluminum wiring carefully designed to safely conduct electricity through the entire string. Each wire is typically 22 or 24 gauge, thin enough to be flexible yet sturdy enough to handle the electrical load. Manufacturers coat these wires with PVC (polyvinyl chloride) or PE (polyethylene) insulation, which provides essential protection against moisture and prevents short circuits.
Modern Christmas light wiring often includes additional features like parallel circuits, which allow the rest of the string to continue working even if one bulb burns out. The insulation comes in various colors to match the overall design, though green and white remain the most popular choices to blend with holiday decorations.
Recent innovations have introduced more eco-friendly insulation materials, responding to environmental concerns while maintaining the same protective qualities. These newer options reduce the environmental impact without compromising the safety and durability that makes Christmas lights last through many holiday seasons.
Bulb Construction
Modern Christmas lights come in two main varieties: traditional incandescent bulbs and LED lights. Traditional bulbs consist of a glass housing filled with an inert gas, containing a tungsten filament that glows when electricity passes through it. These bulbs are manufactured by forming glass into the familiar teardrop or round shape, inserting the filament, and sealing the base with metal contacts.
LED Christmas lights, on the other hand, are built using semiconductor materials that emit light when electrical current flows through them. These lights are typically encased in epoxy resin or plastic, making them more durable than glass bulbs. The manufacturing process involves placing tiny LED chips on circuit boards, connecting them with fine wires, and encasing them in their protective housing.
While traditional bulbs are simpler in construction, LED lights are more complex but offer superior energy efficiency and longevity. Their solid-state construction also means they’re less likely to break during handling and storage, making them an increasingly popular choice for holiday decorating.
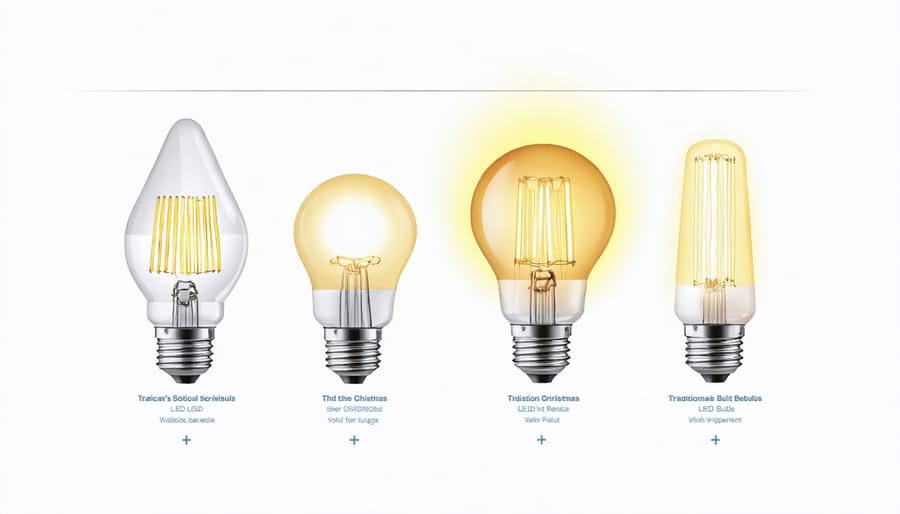
The Manufacturing Process
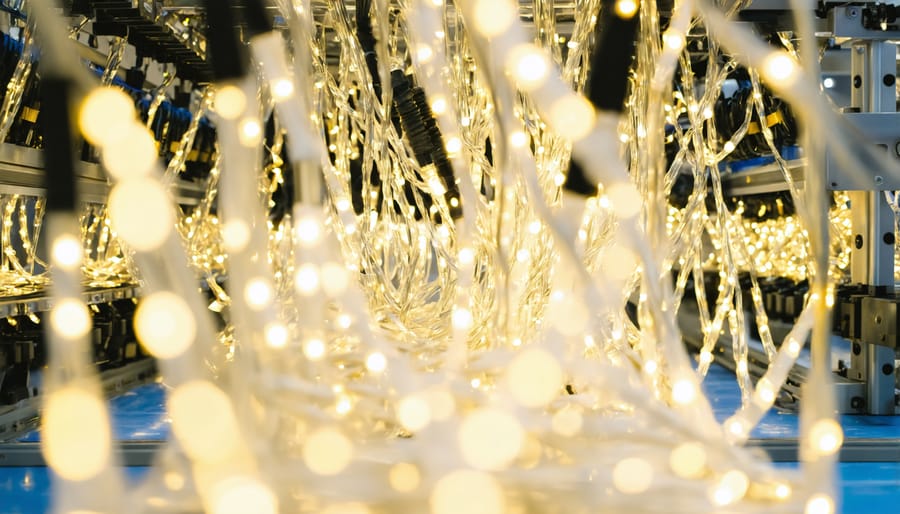
Circuit Board Creation
The heart of modern Christmas lights lies in their carefully designed circuit boards, which control everything from basic on/off functions to complex color-changing patterns. These compact electronic components start as copper-traced boards, where precise pathways are etched to create electrical connections. Manufacturers use automated machines to place tiny surface-mount components, including LED drivers, resistors, and microcontrollers, onto these boards with remarkable precision.
For traditional steady-burning lights, the circuit design is relatively simple, focusing on power distribution and voltage regulation. However, many contemporary Christmas lights feature advanced circuitry that enables features like dimming, twinkling, or synchronized light shows. These sophisticated boards include programmable chips that store lighting patterns and timing sequences.
The assembly process involves wave soldering, where the boards pass through a wave of molten solder to secure all components in place. Quality control systems then test each board for proper electrical connections and functionality. To protect against moisture and environmental factors, the completed circuits are sealed with a weather-resistant coating.
Energy efficiency is a key consideration in modern circuit design, with manufacturers incorporating power-saving features like voltage regulators and current limiters. These components ensure the lights operate at optimal efficiency while maintaining their intended brightness and performance, contributing to lower energy consumption during the holiday season.
Final Assembly and Testing
Before Christmas lights make their way to store shelves, they undergo rigorous quality control and safety testing. Each strand passes through multiple inspection points where trained technicians verify the proper functioning of every bulb and connection. The lights are tested for voltage consistency, ensuring they operate safely within standard household electrical systems.
During the final assembly stage, workers carefully attach lamp holders to the main wire and secure the bulbs in place. Each connection point is checked for proper insulation to prevent short circuits and potential safety hazards. The lights then move through automated testing stations that simulate various environmental conditions, including temperature changes and moisture exposure.
Safety certification is a crucial part of the process. Manufacturers must meet strict standards set by organizations like UL (Underwriters Laboratories) and ensure their products comply with international safety regulations. The lights undergo stress tests to verify their durability during typical holiday usage conditions.
Quality control teams also check for aesthetic consistency, ensuring uniform color distribution and brightness levels across each strand. Any units showing signs of defects or inconsistencies are removed from production. The final step involves packaging the lights with clear instructions for safe installation and use, along with important safety warnings and energy-saving tips for consumers.
This thorough testing process helps ensure that the Christmas lights you bring home are both safe and reliable for many holiday seasons to come.
Energy Efficiency Comparisons
Traditional vs LED Energy Usage
The shift from traditional incandescent Christmas lights to LED alternatives represents one of the most significant advances in holiday lighting technology. While traditional incandescent bulbs consume around 7 watts per bulb, modern LED Christmas lights use merely 0.1 watts, resulting in a dramatic 95% reduction in energy usage. This efficiency translates directly into opportunities to reduce your energy bills during the holiday season.
For perspective, a typical 100-light string of traditional bulbs consumes about 40 watts per hour, while an equivalent LED string uses only 5 watts. Over a holiday season of 30 days, with lights operating 6 hours daily, traditional lights might cost around $25 to operate, compared to just $3 for LEDs. Beyond the immediate cost savings, LED lights also last significantly longer – up to 25,000 hours compared to 3,000 hours for traditional bulbs.
This dramatic difference in energy consumption not only benefits homeowners financially but also contributes to reduced environmental impact during the festive season, making LED lights an increasingly popular choice for environmentally conscious consumers.
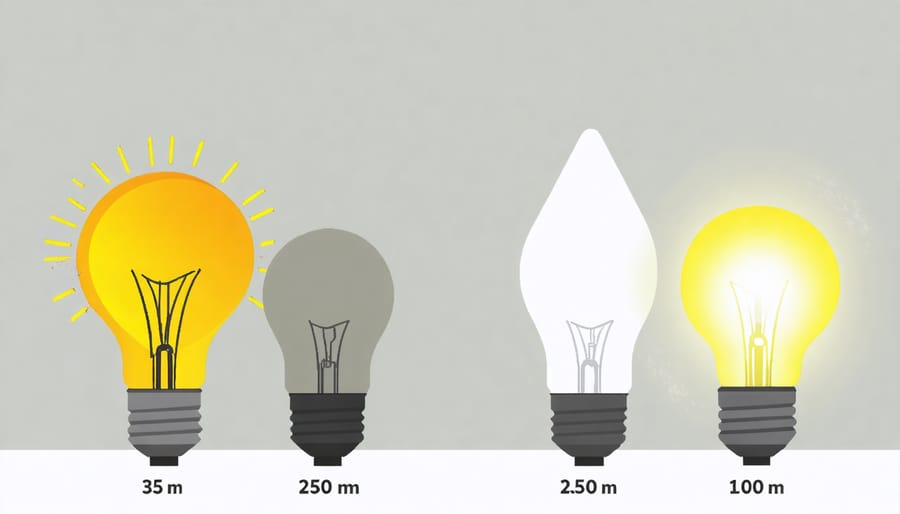
Solar-Powered Options
As consumers become more environmentally conscious, manufacturers have developed solar-powered Christmas lights that offer a sustainable alternative to traditional plug-in varieties. These eco-friendly options feature small solar panels connected to rechargeable batteries, typically using nickel-metal hydride (NiMH) or lithium-ion technology.
The manufacturing process differs from conventional lights primarily in the integration of photovoltaic cells and weather-resistant housing. Solar lights include specialized circuitry that manages power collection during daylight hours and automatically triggers illumination at dusk. Most models incorporate LED bulbs for maximum energy efficiency and longevity.
Production typically involves assembling miniature solar panels using silicon cells, connecting them to efficient charge controllers, and housing everything in UV-resistant plastic casings. Manufacturers often include light sensors and timing circuits to optimize performance. The latest models feature improved battery storage capacity and more efficient solar collectors, allowing for longer operating times during winter months when daylight is limited.
These sustainable alternatives eliminate the need for external power sources while reducing both energy costs and environmental impact, making them an increasingly popular choice for eco-conscious holiday decorating.
Environmental Impact and Sustainability
The manufacturing of Christmas lights has significant environmental implications, particularly in terms of resource consumption and waste management. Traditional incandescent Christmas lights require substantial energy and raw materials during production, including copper, glass, and various plastics. However, the industry has made remarkable strides toward sustainability with the widespread adoption of LED technology.
LED Christmas lights not only contribute to better home energy efficiency during use but also have a smaller environmental footprint during manufacturing. They require approximately 70% less energy to produce compared to traditional bulbs and use fewer raw materials overall.
Many manufacturers are now implementing closed-loop production systems, recycling defective products, and using recycled materials in packaging. Some companies have also switched to water-based paints and lead-free solder, reducing harmful chemical emissions during production.
The disposal of Christmas lights presents another environmental challenge. While most components are recyclable, many strings end up in landfills. Fortunately, numerous recycling programs now specifically accept holiday lights, processing them to recover valuable metals and plastics for reuse in new products.
Consumers can contribute to sustainability by choosing LED lights from manufacturers with strong environmental practices, properly maintaining their light strings to extend their lifespan, and recycling old sets through appropriate channels. Some retailers even offer trade-in programs, providing discounts on new LED strings when customers return old ones for recycling.
By making informed choices about holiday lighting, homeowners can enjoy festive decorations while minimizing their environmental impact and supporting more sustainable manufacturing practices.
As we’ve explored the fascinating journey of Christmas light manufacturing, it’s clear that both technology and environmental consciousness play crucial roles in modern holiday lighting. Today’s LED Christmas lights represent the perfect blend of tradition and innovation, offering superior energy efficiency while maintaining the warm, festive glow we all love.
To make your holiday display both magical and eco-friendly, consider switching to LED lights, which use up to 90% less energy than traditional incandescent bulbs. Look for lights with the ENERGY STAR certification, and opt for timers to automatically control your display’s operating hours. When purchasing new lights, choose quality over quantity – well-made lights last longer and reduce waste.
Remember to properly store your lights after the holidays to extend their lifespan. Wrap them carefully around cardboard or use storage reels to prevent tangling and damage. If your old lights stop working, check with local recycling centers about proper disposal methods, as many components can be recycled and repurposed.
By making informed choices about our holiday lighting, we can maintain cherished traditions while protecting our environment and reducing energy costs for years to come.